davemartin88
Full time employment: Posting here.
- Joined
- Aug 26, 2008
- Messages
- 812
I posted a picture of a lithopane in another thread and had a couple of people ask about some more examples- this is the latest carving I did today. I'm using a software program called PhotoCarve to convert a photo in to a format that can be fed to my computerized router. I've just started learning about these but has been a lot of fun. The carving is done on to a 1/4" thick piece of white Corian counter top material, once it's carved, a light from the back will reveal most, if not all of the original details of the original photo assuming you made the conversion correctly.
This one took about 3 hours for the machine to carve. I started it carving and then went off to cut and split some trees I've taken down to open up our view, stopped every 30 minutes or so to check on progress.
The puppy is named Sparky, he was a foster dog that DW and I took care of last summer before finding him a home. He's deaf so presented a few challenges with training but we really fell in love with him. He is the center of attention in his new house- he turned out to be a really nice looking dog but is pretty large (not obese, just big!) for a sheltie- he just kept growing and growing! Guess he couldn't hear anyone telling him that he was getting too big to be a sheltie. His mom and dad weren't unusually big so just one of those things.
Anyway, here are two pictures, first one is the carving just off the machine, doesn't look like much.
This one shows what it looks like after a light is shined on the back, working on some wood boxes to frame the carvings and hold some LED lights. Enjoy.
This one took about 3 hours for the machine to carve. I started it carving and then went off to cut and split some trees I've taken down to open up our view, stopped every 30 minutes or so to check on progress.
The puppy is named Sparky, he was a foster dog that DW and I took care of last summer before finding him a home. He's deaf so presented a few challenges with training but we really fell in love with him. He is the center of attention in his new house- he turned out to be a really nice looking dog but is pretty large (not obese, just big!) for a sheltie- he just kept growing and growing! Guess he couldn't hear anyone telling him that he was getting too big to be a sheltie. His mom and dad weren't unusually big so just one of those things.
Anyway, here are two pictures, first one is the carving just off the machine, doesn't look like much.
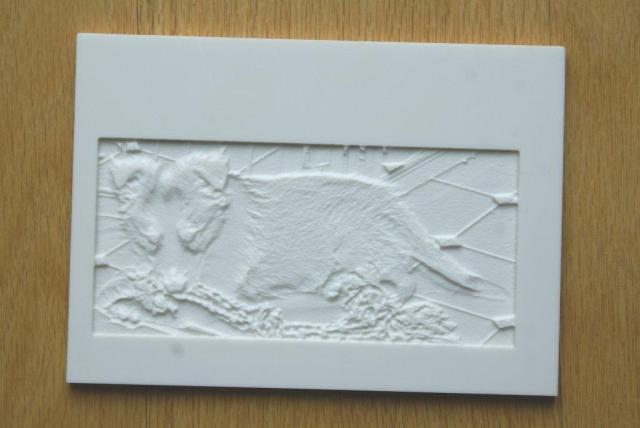
This one shows what it looks like after a light is shined on the back, working on some wood boxes to frame the carvings and hold some LED lights. Enjoy.
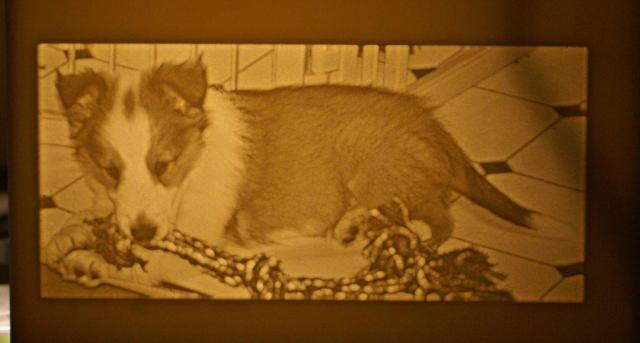